This session spotlights groundbreaking case studies in sustainable bioprocessing where we will hear from companies implementing innovative practices to reduce their environmental impact. These real-world examples showcase how the bioprocessing sector is evolving to meet sustainability goals without compromising product quality or safety.
Horizon 2030 at Ipsen Wrexham.- James Nicholls
An exploration of how Ipsen’s global Horizon 2030 initiative is being implemented at Ipsen Wrexham, looking at how understanding our energy utilisation has been converted into projects delivering benefits.
Intelligent Cleanroom Control System - Alan Robertson
The EECO2 Intelligent Cleanroom Control System (ICCS®) installed at the CPI Medicines Manufacturing Innovation Centre (MMIC) represents a significant advancement in cleanroom technology, focusing on energy efficiency and sustainability. The ICCS® is designed to reduce energy consumption in cleanrooms by up to 70% through adaptive and demand-based control of airflow rates, addressing the high energy demands typically associated with cleanroom environments.
Cleanrooms consume significantly more energy than standard office spaces due to the constant need for high air change rates to manage contamination. The ICCS® tackles this issue by dynamically adjusting the airflow based on real-time contamination data and environmental parameters such as temperature, humidity, and pressure differential. This system ensures compliance with cleanroom standards while optimizing energy use, thus supporting sustainability goals and reducing operational costs.
At CPI MMIC, the ICCS® is part of a broader initiative to enhance pharmaceutical manufacturing processes through innovative technologies. The Centre, a collaboration involving CPI, the University of Strathclyde, and industry partners like GSK and AstraZeneca, aims to revolutionize drug development and production with a focus on sustainability and efficiency. The ICCS® installation aligns with these goals by providing a cleaner, more energy-efficient environment for pharmaceutical manufacturing, ultimately contributing to the Centre's mission of reducing the carbon footprint of drug production.
RO membrane WFI generation system - Chris Davies
At the conference we are presenting on our new water for injections (WFI) generation system that utilises Reverse Osmosis (RO) membrane technology. This method of WFI generation does not require a change of state – heat to generate this material. This technology has been approved by the MHRA for use within Pharmaceutical manufacturing since 2016 – however uptake within the industry has been slow. This technology offers businesses an improved sustainability profile due to the reduce energy consumption. Our belief at CGTC is that by undertaking the installation, qualification and performance testing of this system we have the opportunity to generate data that could lead to a wider adoption of this technology and the realisation of the sustainability benefits.
Surprising Sustainability Benefits of Electronic Batch Records - Andrea Pearson
In April 2022 FDBK’s Billingham Site moved to electronic batch records from paper, in the Mammalian Cell Culture Asset. The main drivers for the project were to increase efficiency, remove documentation burden and encourage a culture of continuous improvement and error prevention. However, there were also some surprising sustainability benefits realised, that when calculated, show the added benefit projects such as these can bring to our net zero ambitions.
Smart Metering within AstraZeneca - Rachel Kelly & Jonathan Furbey-Taylor
This presentation will provide an overview of how AstraZeneca is implementing smart metering across manufacturing sites in their global network, with the aim of reducing energy consumption by leveraging insight that is provided through data visualisation to implement changes across the network that continuously drives down consumption and reduce their global footprint.
×
David Gruber
Ipsen Biopharm Ltd
David joined IPSEN in April 2017 and is currently Senior Director, Bioprocess Sciences. He brings in excess of 20 years’ experience in bioprocess development, tech transfer and cGMP manufacturing for biopharmaceutical products. Prior to joining Ipsen David spent 10 years working at MedImmune and 5 years at Xenova developing manufacturing processes for early and late phase clinical products. David’s expertise spans platform and novel technology development, process / product understanding and application of multivariate analysis. More recently his keen interest in sustainability has seen him engage in Ipsen’s sustainability programs, supporting both Engineering and Procurement activities. In 2023 David volunteered to lead the Manufacturing Advisory Committee’s Sustainability working group.
×
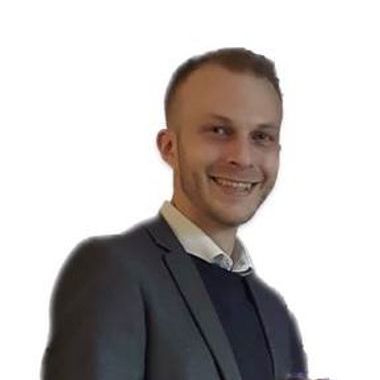
Chris Davies
Project Engineer, Cell & Gene Therapy Catapult
I am a project engineer currently working for Cell and Gene Therapy Catapult (CGTC), where we are delivering site wide redevelopment to support collaborators with large scale cell and gene therapy research and development. The site was previously manufacturing animal vaccines. The redevelopment works looks to realise the potential of the site as a GMP manufacturing innovation hub to support the growing bioprocessing industry within the UK. I have worked within the cell and gene therapy GMP manufacturing space since 2017. Previous roles have included the design and build of gene therapy manufacturing facilities, maintenance engineering support for gene therapy production as well as process engineering support and project management. This has given me a broad understanding of the engineering support companies require to be able to safely manufacture these novel medicines that aim to cure diseases. Prior to my current appointment I have delivered clean room construction project management across the manufacturing sector for space, bioprocessing, imaging, micro electronic and technology sectors.
×
Jonathan Furbey-Taylor
Global Sustainability Project Leader, AstraZeneca UK Ltd
Jonathan Furbey-Taylor is a Global Sustainability Project Leader at AstraZeneca, implementing changes across the business that deliver AstraZeneca’s sustainability ambitions. This includes leading the global rollout of data visualisation from Smart Metering data, as well as leading the transition of AstraZeneca’s global fleet to 100% EV where technically possible. Prior to this role, Jonathan has worked in project management and leadership roles across various industries including Retail, Consumer Services and E-Commerce.
×
Rachel Kelly
Global Sustainability Project Leader, AstraZeneca UK Ltd
Rachel Kelly is a Global Sustainability Project Leader within AstraZeneca, leading a diverse range of projects across AstraZeneca’s sustainability program. This includes leading the Operations workstream for Access to Healthcare, as well as leading the Scope 3 program to ensure delivery of key attributes of AstraZeneca’s Ambition Zero Carbon targets. Within her current role, Rachel is also responsible for managing the early careers and talent team within Global SHE (Safety, Health & Environment). Prior to this role, Rachel has spent 10 years at the site in Macclesfield working in various Supply Chain leadership roles.
×
James Nicholls
Lead Project Engineer, Ipsen Biopharm Ltd
James joined Ipsen in October 2023 and is currently a Lead Project Engineer working on the site’s capital investment projects including sustainability driven initiatives.
James is new to the pharmaceutical sector having previously spent 10 years delivering projects in the food and drink industry following completion of a MEng in Chemical Engineering.
×
Andrea Pearson
Operations Engineering Manager, Fujifilm Diosynth Biotechnologies
Andrea is the Operations Engineering Manager at FUJIFILM Diosynth Biotechnologies in Billingham, UK and has responsibility for all maintenance on site. She is a Chartered Chemical Engineer who has worked for over 16 years in the Petrochemical and now Biotechnology industries. Her career has included Operations Management of Upper Tier COMAH sites, Manufacturing Excellence Improvement Projects and Turnaround Management. In 2021 she moved to FUJIFILM Diosynth Biotechnologies, firstly working as Technical Operations Manager for the Mammalian Cell Culture Manufacturing assets and then into Maintenance Management. Andrea was named one of the WES Top 50 Women in Engineering 2021 and is passionate about encouraging women into STEM careers and striving towards more sustainable manufacturing.
×
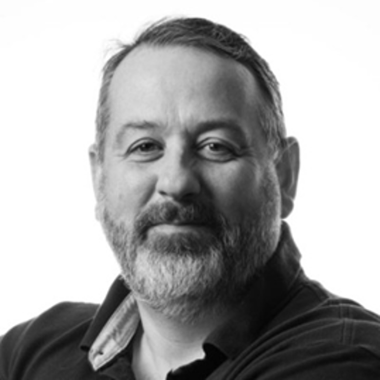
Alan Robertson
Head of Operational Engineering, Medicines Manufacturing Innovation Centre
Alan Robertson is the Head of Operational Engineering at CPI's Medicines Manufacturing Innovation Centre. With a diverse background spanning military service and pharmaceutical engineering, Alan brings a wealth of experience to his role. Alan served 23 years in the Royal Navy as a Weapons Engineering Mechanic (Ordnance) specializing in submarines. His career culminated as a Facilities Manager and Instructor at the Royal Navy Strategic Systems School in Faslane, where he delivered training on the Trident Weapon System using a state-of-the-art £50M simulator. Following his military service, Alan transitioned to the medical devices and pharmaceutical industry. Over 15 years, he held various positions in GMP facilities as Engineering Manager and Facilities Manager. Prior to joining CPI in May 2021, Alan served as the Engineering/Facilities Manager at Curia in Glasgow, where he successfully managed three major cleanroom facility overhauls. Outside of work, he is an avid fly fisher and whisky enthusiast.