bioProcess UK insight: Transforming biomanufacturing through the first single-use cell culture facility in the UK
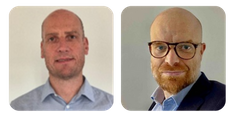
In this blog, John Stewart, Vice President of KojoX Strategy and Rasmus Pedersen, Associate Director of Process Technology for FUJIFILM Diosynth Biotechnologies, talk about FUJIFILM's flagship single-use cell culture facility in Billingham, UK.
The biomanufacturing sector is set to continue its upward trajectory, with global demand for mammalian cell culture capacity growing at nearly 11.5% per year1. And most biopharmaceutical companies are outsourcing production services to contract development and manufacturing organizations (CDMOs). The introduction of innovative technologies, diverse product offerings, and expanded applications have driven CDMOs to make significant capital investments to increase mammalian cell culture capacity to enable the flexibility and agility needed to adapt to rapidly changing market demands. As a potential therapeutic progresses through its lifecycle, flexible manufacturing solutions are essential for effective demand management. This includes the ability to scale up or out during preclinical, clinical, and commercial production stages, or even to scale down at the end of the product lifecycle.
Modularity of KojoX™ enables flexible scalability and rapid responsiveness to expand network capacity
FUJIFILM Diosynth Biotechnologies (FDB) is taking this a step further by moving beyond the traditional CDMO business model. Through its Partners for Life® commitment, FDB is investing heavily to build a globally integrated network—spanning the US, UK, Denmark, and Japan—of modular process and manufacturing facilities to support customers’ entire pipelines, from pre-clinical to commercialization1,2. Expansions of existing facilities and new construction projects are underway to grow network capacity for cell culture and microbial production.
Central to this Capital Expansion strategy is FDB’s KojoX, a paradigm-shifting operational philosophy to disrupt the status quo in biomanufacturing. KojoX is an ecosystem of manufacturing assets across sites, scales, and modalities, with harmonized facility designs, equipment, processes, and procedures, to support the development and manufacturing of life-changing medicines as they move through the regulatory process quickly and efficiently. This modular design can be adapted quickly to multiple manufacturing strategies (scale out or scale up) while future-proofing infrastructure for rapid capacity additions, as needed. Creating an end-to-end network that spans a medicine’s full product life cycle accelerates tech transfers, shortens time-to-market, and enhances supply chain resilience with increased geographic diversity. Clients can enter the value chain at any stage of development and leverage modular solutions tailored to their needs. This approach eliminates the risk of investing in capacity they do not need while providing the advantage of low risk and fast access to manufacturing capacity.
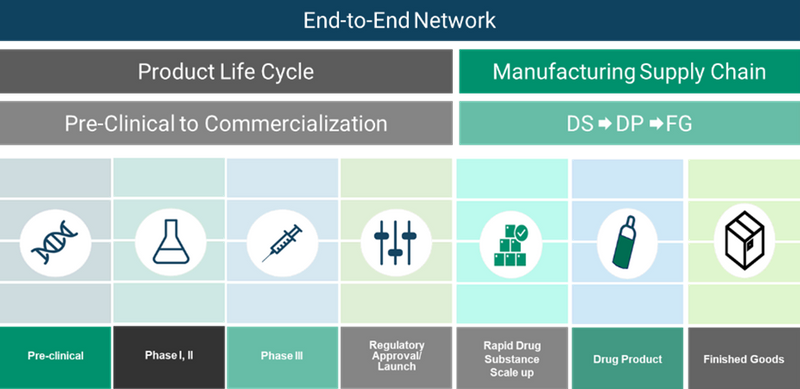
Flexible single-use cell culture facility: flagship KojoX™ facility in the UK
FDB’s Billingham, UK site is the flagship of the KojoX operational model in the single-use cell culture network, representing a strategic move towards adaptability and responsiveness in the ever-evolving biopharmaceutical industry. The 10,000 m2 expansion over 3 floors (Figure 2) will grow FDB’s mammalian cell culture process development and manufacturing capabilities. The facility will provide, a versatile GMP site with full segregation and unidirectional product flow to support a range of cell culture-based products, primarily focused on mAbs, with potential future expansion to include viral gene therapy. This facility is being designed to support programs from early through late-stage clinical development into full commercial manufacturing.
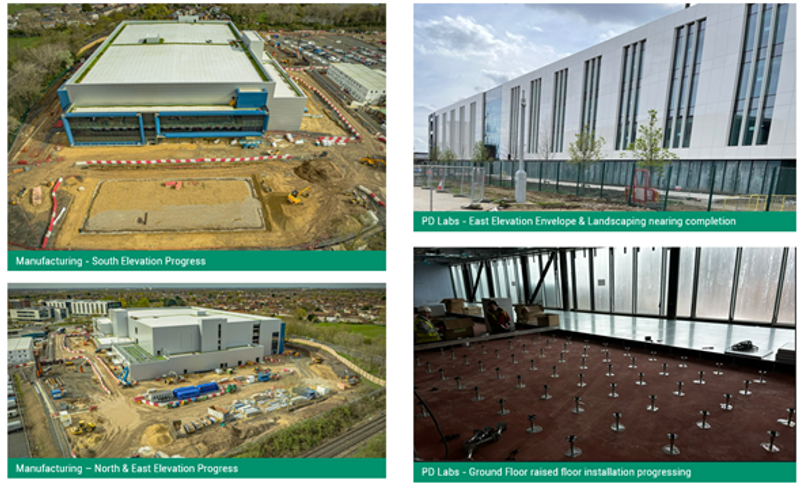
Implementing a KojoX modular approach, flexible standard ‘lanes’ will be built using the equipment that best fits product and process needs. This facility will be equipped with modular units of 2,000 L and 5,000 L single-use bioreactors, designed for easy mobility. These bioreactors can be wheeled in and out to support closed-process operations for mammalian cell culture. Figure 3 illustrates a product flow that includes inoculation, cell expansion, cell culture and three drug substance purification suites per lane with both small and medium production lanes available. Utilizing this modular approach enables flexible scale-out and scale-up/down manufacturing strategies tailored to each batch. It also provides access to adaptable production lines and reduces start-up costs. The small lane can accommodate capacities up to 2,000 L and the medium lane could offer two capacity configurations: 3 x 5,000 L or 2 x 2,000 L bioreactors.
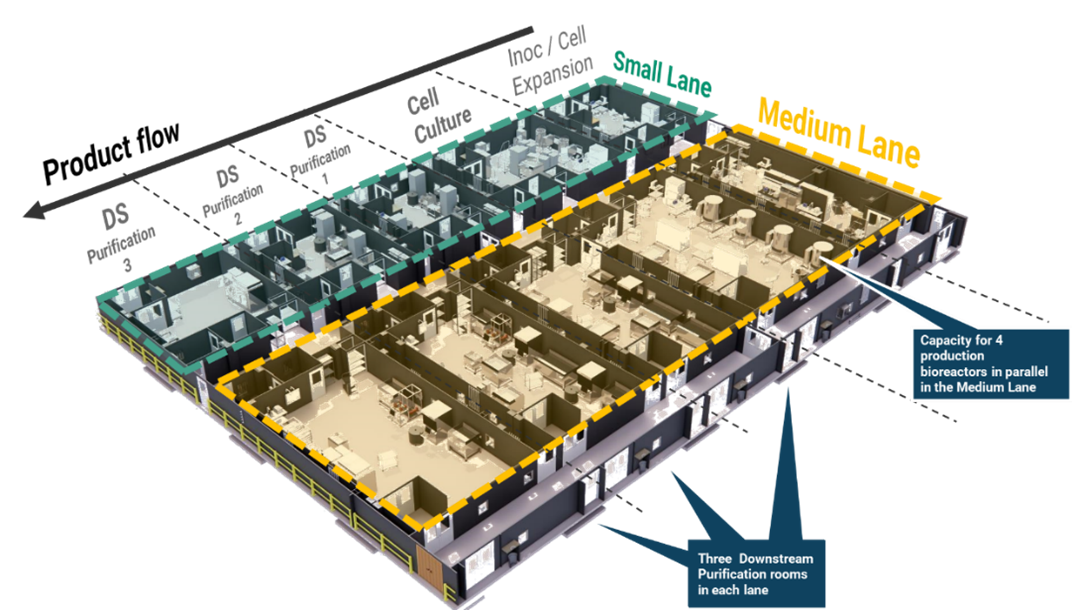
In addition, the network’s single-use design supports multiplexed scale-up and scale-out strategies and will include the flexibility to feed into large-scale, commercial 20,000 L production bioreactors. This enables programs to be sited at any facility within the network without additional tech transfers. The approach ensures access to capacity across the entire product lifecycle—from development and clinical phases to commercialization—regardless of scale or location, supported by robust control strategies and centralized data collection systems1.
Partners for Life®
The KojoX™ modular approach, combined with FDB’s depth of expertise in drug substance development and manufacturing, ensures right-first-time product delivery. This approach offers the flexibility and agility needed to adapt to the rapidly changing market. FDB’s partnership-based business model coupled with its growing end-to-end global network, and a steadfast commitment to continuous innovation, uniquely positions the company to help clients bring new medicines to market faster - ultimately benefiting patients.
References
1. Gonzalez F and Emily L. Transforming the Biopharmaceutical Industry: Addressing Patient Access to Medicines with Interconnected Networks. Fujifilm Diosynth Biotechnologies. https://fujifilmdiosynth.com/knowledge-center/resource-library/transforming-the-biopharmaceutical-industry-addressing-patient-access-to-medicines-with-interconnected-networks/ Accessed November 11, 2024.
2. Pedersen, R. FUJIFILM Diosynth Biotechnologies Capacity Update October 2024: Large Molecule Drug Substance. Fujifilm Diosynth Biotechnologies. Published October 22, 2024. https://www.outsourcedpharma.com/doc/fujifilm-diosynth-biotechnologies-capacity-update-october-large-molecule-drug-substance-0001 Accessed November 11, 2024.