BIA MAC LeaP: A Journey of cross-sector learning
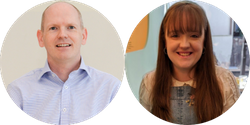
This year, we're celebrating a big milestone... More than 100 participants in the BIA's Manufacturing Advisory Committee (MAC) Leadership Programme (LeaP)! Roger McGilvray and Louise Taylor were participants in the 3rd cohort of LeaP. Roger is Director of Allogeneic Process & Analytical Development at Adaptimmune, and Louise is RNA Training Academy Lead at CPI.
In this blog, Roger and Louise share their experience of the third cohort of the BIA MAC LeaP. They focus on the benefits of cross-sector learning from site visits and developing peer networks.
Background
Back in March 2019 we got together for our first site visit to GE (now Cytiva) at the Pollards Wood office. This was our first proper chance to get to know each other after the initial intro at the BIA offices in London. During the London session we touched upon some potential ideas for projects, but it wasn’t until we had our first site visit that we could really spend time fleshing out the idea of what we would do during the two-year programme. This is when we decided we would look at what we can learn from other businesses, and although we were agreed this is what we wanted to do, there was a lot of uncertainty as to whether it would work or turn into something beneficial.
Fast forward 4 years, and we certainly did find these additional visits useful and enjoyable, and they turned out highly successful. All the visits were enlightening in some way, to see how these other business areas operate and innovate. This is not to take away from the site visits themselves which provide a much ‘closer-to-home’ view of operation. External visits which are geared towards learning is a great way to provide additional development opportunities, as we want to challenge and widen the thought process as we look at solutions for our everyday problems. These visits were successful as they allowed us to be immersed into a different sector for the day and see they ways in which they work and the similarities or differences to our industry.
Summary of site visits
Adaptimmune : BMW Mini Plant, Oxford
The tour of the Oxford BMW Mini Plant is open to the public and they can offer a private tour session for groups. All cars are made to customer order and the plant makes between 800-1000 cars a day, using a ‘just-in-time’ logistics set up to assemble the cars which then go out by road and rail to their new owners.
GSK: Airbus Defence & Space, Stevenage
The Stevenage site is primarily directed towards manufacture of satellites, but is also home to the Mars Rover Vehicle, built in a state-of-the-art bio-clean facility. The satellite manufacture is very low throughput, with around 4 per year being made, so their quality control seemed very odd to us but the chances of a mistake or mix up progressing through this process is extremely low. The quality of the final product must be very high as there is no opportunity for a quick service visit once in operation.
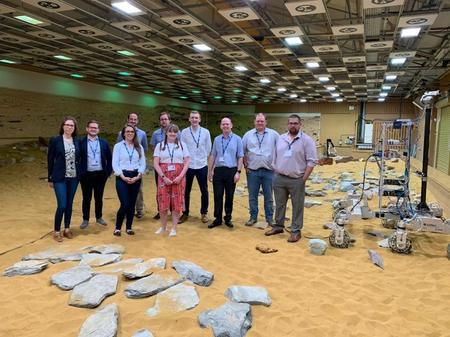
CPI: Quorn Foods, Billingham
Quorn, as most will know, makes a high protein meat substitute. This is mycoprotein from filamentous fungi grown in a 150-ton bioreactor, about 10 storeys high, which we were allowed to climb to the top of, using stairs before you have images of us scaling giant bioreactors. The process used has been in place for many years with little change other than increasing the amount of automated monitoring and control. This suggests that when you have a manufacturing process that is working well, leave it alone. However, increasing demand for sustainable living means that some process development is required to see what optimisation potential is possible to get higher yield, or reduce the bioreactor size. Whilst this process was closer to our industry it allowed us to envisage how manufacturing reaches steady state.
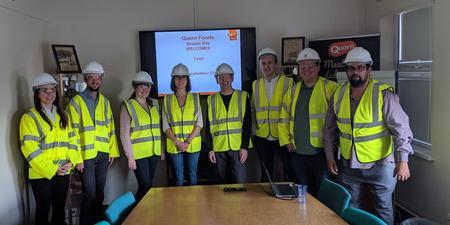
Synpromics (part of AskBio): Nairns, Edinburgh
We visited the Nairns factory at their Bonnyrigg facility, which is where they make all of their gluten-free oatcakes, sweet biscuits, crackers, flatbreads, snacks and cereals. We were able to follow their biscuit production process from ingredient warehouse to packaged product and provided great insight into running an automated process with low staffing requirement. An interesting innovation was an extending section of the manufacturing line to allow troubleshooting without having any of the biscuits burning during downtime. All of us would have been happy to take on a taste tester role at the facility.
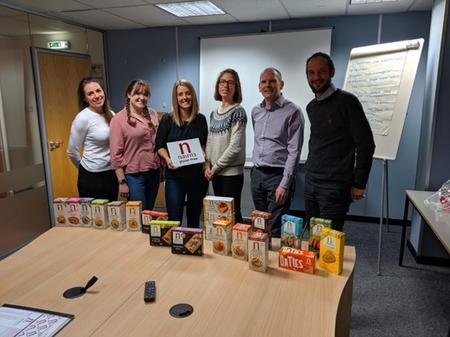
Exmoor Pharma : NHSBT, Filton Blood Centre
You would never imagine when attending a blood donation session that the blood then goes to a centre to be processed in such a way. Filton is the NHSBT blood processing facility covering Southwest of England, and processes a large number of blood donations each day. The learning from this visit is the way donations are batch processed. The blood cannot be continuous as it comes from blood donation sessions that take place during regular daytime and early evening. This means that the staff need to be multi-skilled in order that they can operate different processing steps, an interesting resourcing challenge.
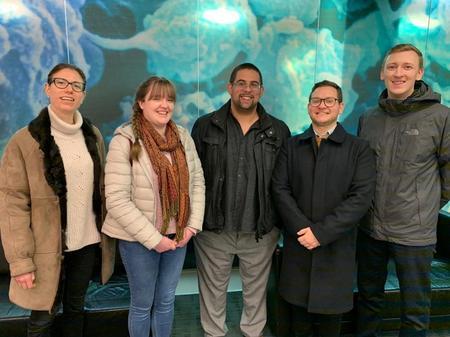
In terms of learnings, we got to see high volume manufacturing at BMW Mini (800-1000 cars per day) versus low volume at Airbus (3-4 satellites per year). We got to see low resource automated processes at Quorn and Nairns. And NHSBT, where they run batch manufacture processing of more than 2000 blood donations a day which brings some interesting challenges.
There were further visits on the schedule, but companies were starting to reduce travel and cutting down on visitors to site as we were progressing, unknown at the time, into lockdown. The intention was to restart but the length of lockdown followed by an extensive period where all our companies had restrictions on visitors was longer than we had initially expected.
End goal and takeaways
The concept was to understand what we could learn from other industries, and we certainly did that. It seems we all refer to specific points in the visits which provided a learning point. One of our groups main takeaways was that being immersed in an alternative industry can help to spark ideas and identify similarities that can then be used to create change and discussion as we’re tasked to move out of our comfort zone. The key themes we identified involved different challenges around logistics, resourcing and innovation are the common aspects that come to the forefront and make us think about application in our own areas of work.
Roger’s reflection on LeaP
LeaP was a great experience for me and so important at the point I was at in my career development. Developing an external peer network was beneficial and I looked forward to each meeting that we had. I still look forward to any opportunities to catch up with my cohort group at the LeaP alumni events and BioProcessUK conference meetings. The experience really broadened my perspective, and I gained a promotion during this time. I would highly recommend participating in the programme.
MAC LeaP is supports the development and training of the next generation of leaders and managers in the biopharmaceutical and cell & gene therapy industries through cross-sector learning and peer networks.